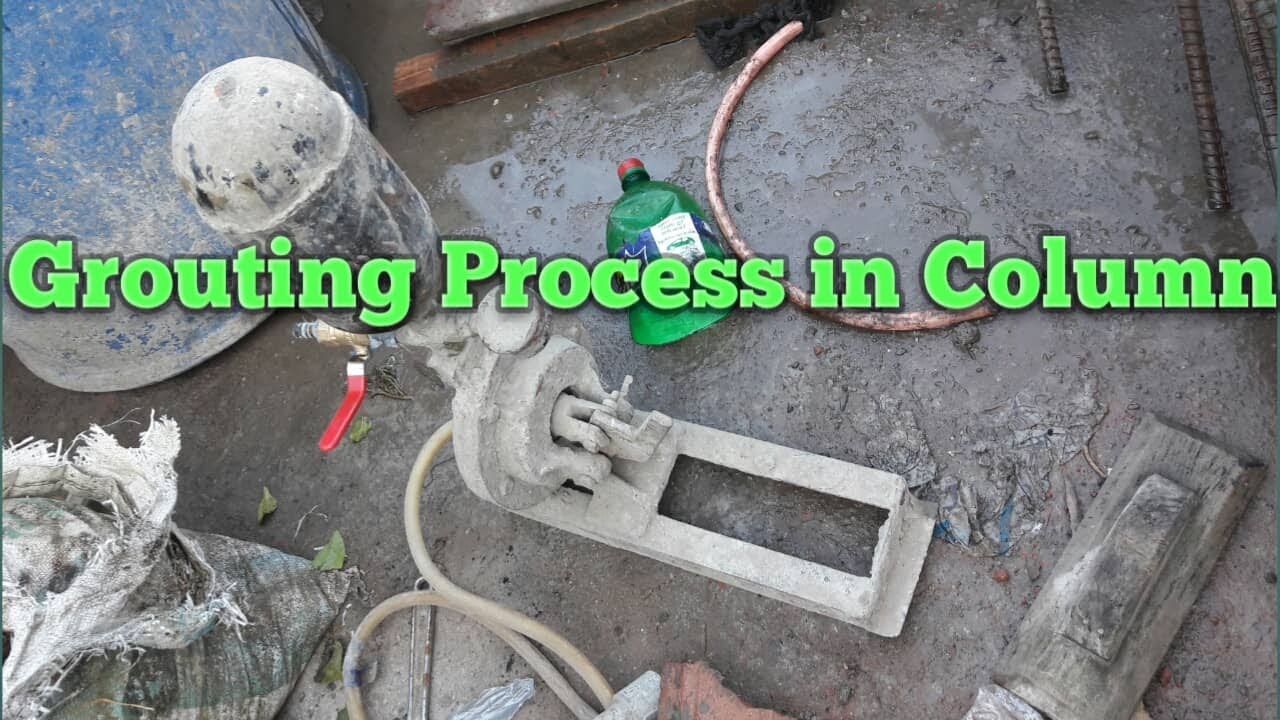
Grouting Process in Column YouTube
The chemical grout is injected under pressure through the ports. The grout permeates the soil and hardens, creating a sandstone-like mass. The grouted soil has increased strength, stiffness, and reduced permeability. Chemical grouting offers the advantages of being easily performed where access and space are limited and no structural connection.
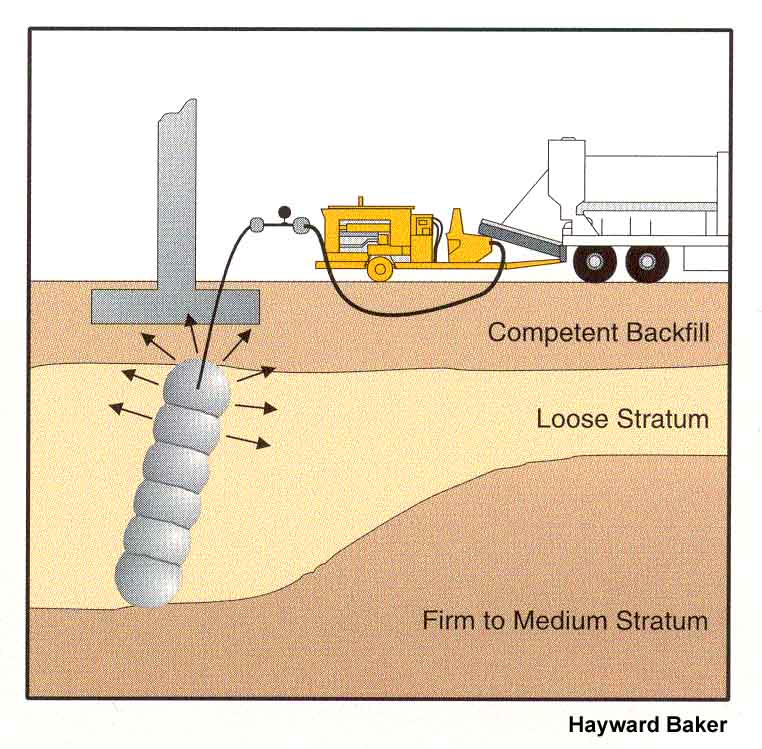
Compaction GroutingGeneral Geotechnical Photo Album
ARDEX ENDURA offers B 30, a cementitious non-shrink grout and B 50, high strength epoxy grout for grouting all kind of machines base plates. Following is the brief table explaining the properties of the grout which helps to select the grout quickly. Cementitious non shrink, expansive grout. B 31 - cementitious grout attains 10N/Sqmm in 10 Hrs.
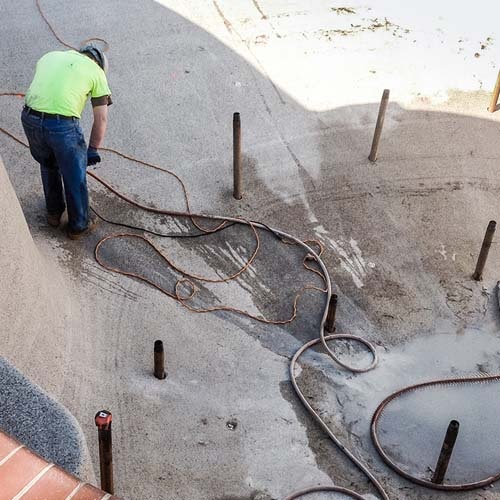
Injection grouting system advantages, methods and applications
This method statement describes the step by step procedure for grouting of machine bases and base plates using the SikaGrout range of ready to use mortar products and shall be read in conjunction with the relevant product data sheet and safety data sheet.

Injection, Grouting and Membrane Works CKTech Ltd
Injection grouting is the method of filling the cracks, open joints, voids, or honeycombs, in concrete or masonry structural members. This is done under pressure with a grout material that cures in place to produce the desired results like strengthening a structure and preventing water ingress.
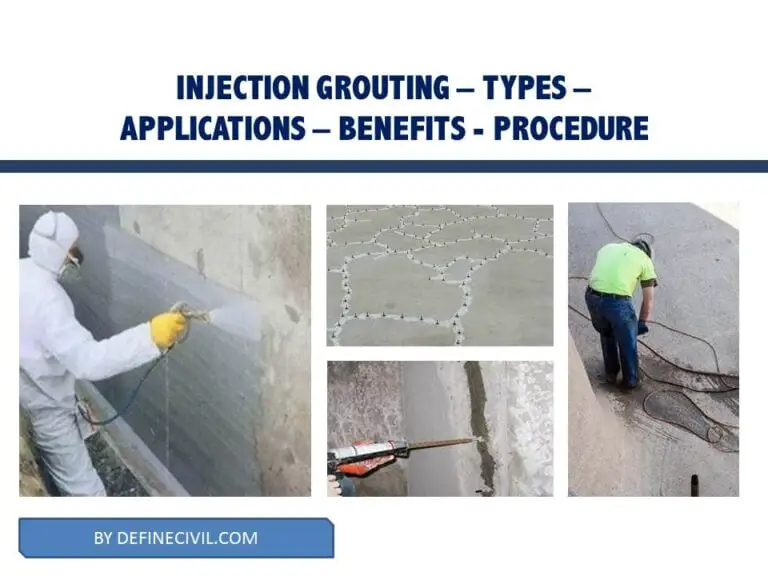
What is injection grouting Purpose Types Procedure Definecivil
Column base plates. General machine base grouting. General grouting where the grout can be exposed to mild or moderate concentrations of many industrial chemicals. If required, the grout can be supplied with Sulphate-Resistant Cement. Most situations where a fluid, sanded grout is needed. Installing anchor bolts or tie rods. ADVANTAGES

(a) Illustration of the jet grouting method; (b) the jet grouting
The bentonite grout is pumped into the annular space through a tremie pipe that has been inserted to the bottom of the borehole along with the casing. The annular space between the borehole and casing is usually 2 inches or larger. This can vary depending on state regulations, depths and drilling conditions. Grouting is complete when the grout.

Grouting Techniques Geotechnical Engineering
Grouting Procedure for Equipment | Base Plate Grouting Purpose: These recommended practices (PIP) are intended to provide recommended procedures, practices and checklist for the installation and pre-commissioning of new and reapplied machinery for petroleum, chemical and gas industry services facilities.

Jet Grouting
Grouting Procedures 1. Drill Ports Drill short holes, which is also known as ports, into the cracks/ openings in order to be used as entry and venting terminals. Minimum diameter and depth of ports are 2.5cm and 5cm, respectively. Spacing between holes is 150 mm c/c for finer cracks to 300 mm c/c for others.
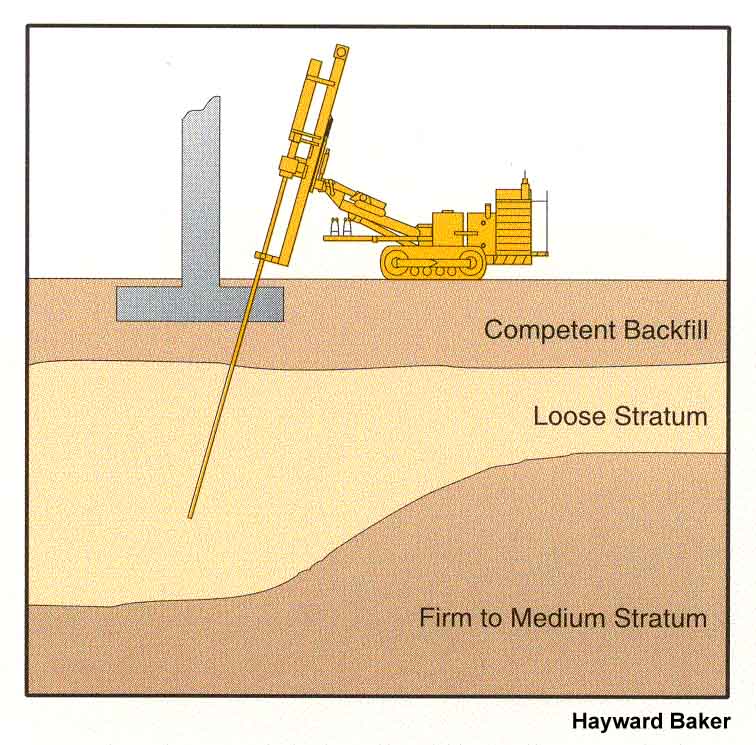
Compaction GroutingGeneral Geotechnical Photo Album
Instructional video on properly grouting a baseplate.Uses Chockfast Red Epoxy GroutFor more information on how to grout rotating or critical equipment system.

PCA Cement Grouting Process YouTube
1. Prepare the Underside With no other actions or specifications, almost no pump or base manufacturer will have the baseplate's underside properly prepared for the grouting procedure. They will have prepared the surface solely to prevent corrosion in the transit and storage stages.

Splitting Action Process of HighPressure Grouting Self Drilling Rock
Grouts are used for different applications like repairing of cracks, filling voids and gaps in tiles, sealing joints for waterproofing of the submerged structure like tunnels, canals etc. and for soil stabilization. Here we are discussing types of grout used for crack repairing. Types of Grouting Based on material, grouts are classified as follows:
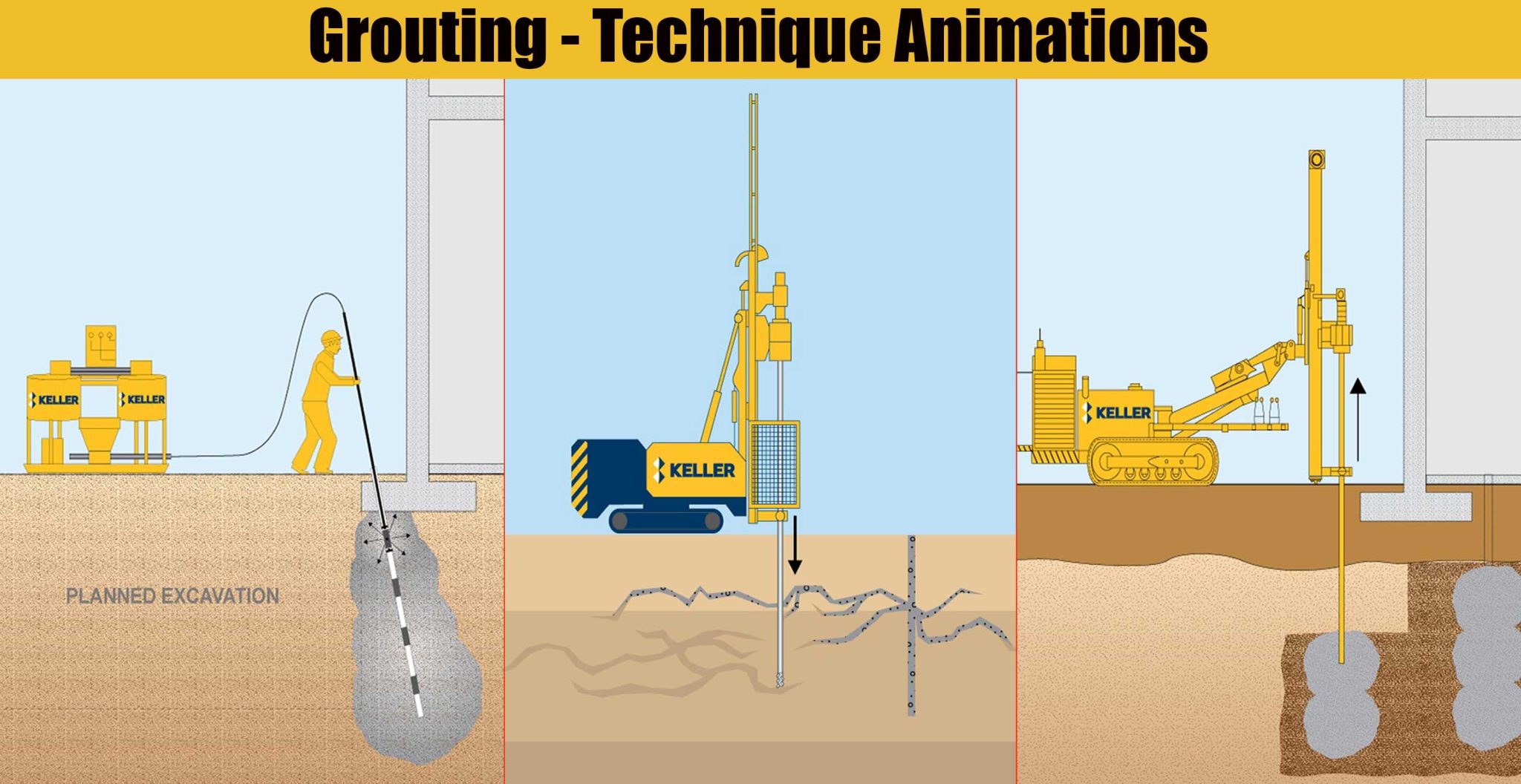
Grouting Technique Animations Engineering Discoveries
Grouting is the process in which materials are injected into cavities or cracks in concrete, masonry structure, soil, and rock mass to increase the structure's load-bearing capacity refer to grouting, and the material used for this process is called grout.
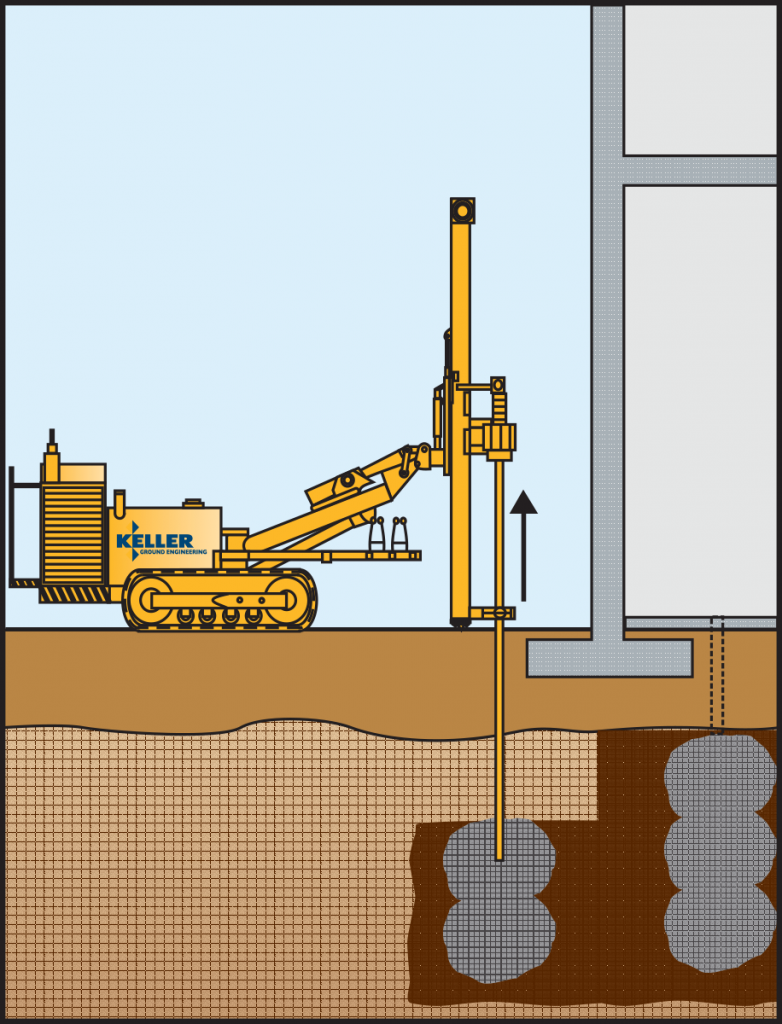
Grouting Process
What Is the Machine Base Plate Grouting Procedure? Properly grouting a sole plate involves the following steps: Preparing the surface of the concrete and the sole plates. Before installation of the grout, the surface of the concrete and the plate must be adequately prepared.

Jet Grouting procedure Download Scientific Diagram
A proper foundation with machine grouting will keep the equipment running longer, while requiring less downtime for maintenance and repairs.. Most grout manufacturers offer specific recommendations on the proper underside preparation materials and procedures. Though cementitious grout was often used in the past, epoxy grouts are now more.
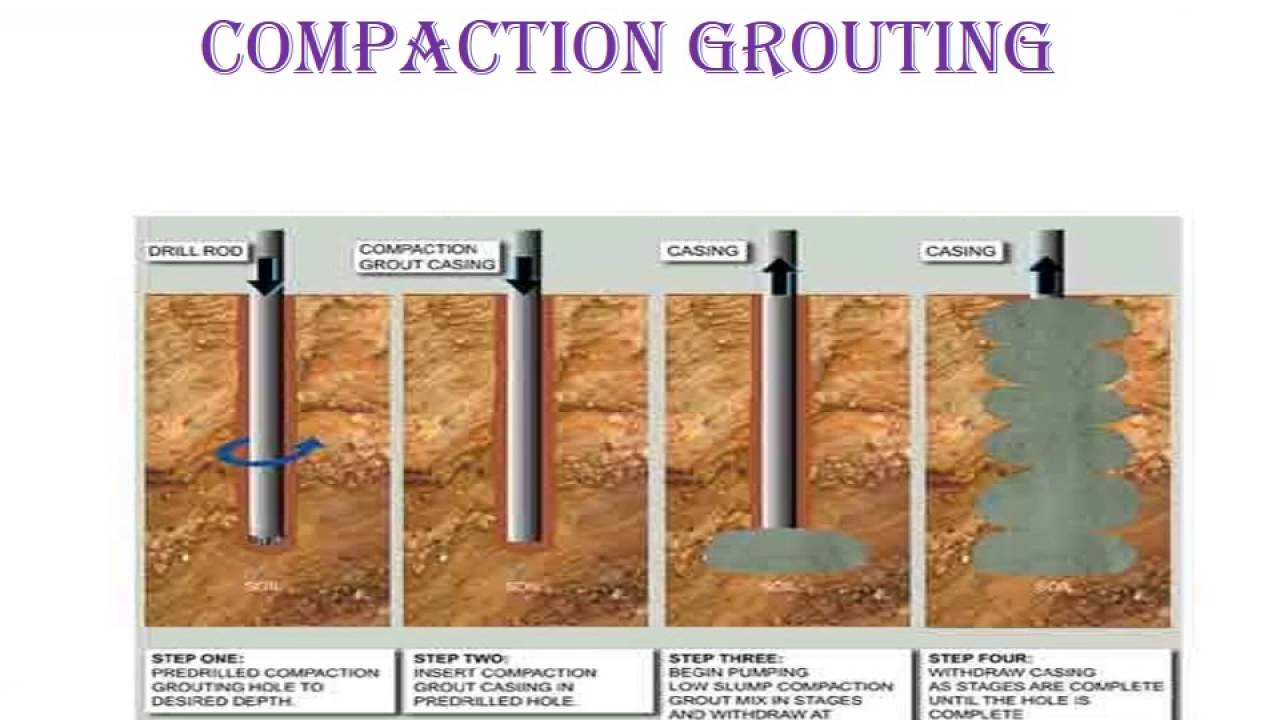
GROUTING YouTube
It is desirable to remove enough old grout from beneath the machine so that a load bearing area equivalent to a rail or sole plate mounting can be provided by the epoxy grout once it has been poured. If the foundation itself is cracked, it should be repaired before proceeding further.. Grouting Procedure for Low-Viscosity Epoxy Grout. 1. The.

jet grouting construction method YouTube
Now the production grout may be mixed and pumped immediately behind the slurry mix, which is thus evacuated from the hose, and may be retrieved in a bucket. Do not attempt to pump production material through a dry hose. One last word about procedures: Occasionally, no matter how conscientious an operator may be, a hose will get plugged.